Reference PROJECTS
Modular Vaccine Facility in a Constrained Urban Setting
Project details
Project details
Client
Confidential Big Pharma
Location
Netherlands
Market
Biologics
Solutions we provided
Modular expansion of the capacity on an existing site. Fill-finish of animal vaccines. Indoor & Outdoor modules
Unique vaccine plant On a difficult site
Unique vaccine plant On a difficult site
When a pharma company wanted to expand one of its European vaccine manufacturing and aseptic filling plants, it turned to KeyPlants for the complex, hybrid project, which used both modular and conventional construction techniques.
To build the two-floor, 1,300-square-meter, biosafety level 2 facility, the client and KeyPlants overcame a number of challenges together.
Site with limited space close to residential area
Site with limited space close to residential area
The site itself was bound on all sides by other buildings and a wall in a residential district just 20 metres away from the neighbouring buildings.
“The site is so small. So, we had almost no space to put our tools, containers, cranes, etc.,” says KeyPlants Project Manager Olle Pettersson. “It was quite complicated to get the modules into this neighbourhood. There were also a lot of restrictions on how much noise we could make.”
"We are proud of our new state-of-the-art modular production facility that enables us to meet our increasing sales volumes. Adding this modular building to our existing production building in limited available space was a great challenge, but nevertheless a successful achievement."
Manager Engineering & Capital Project Lead
State-of-the-art VHP system with complex automation challenges
State-of-the-art VHP system with complex automation challenges
By far the biggest challenges came from the advanced automated Vaporized Hydrogen Peroxide (VHP) decontamination system that Olle thinks may be the first of its kind in the world.
To give some idea of the complexity of the facility, Olle explains that not only are there many separate cleanrooms, but each of these rooms also needs to have its own airlock and its own pressure and temperature environment. “You have very advanced duct work and fans all over the place to control each room separately,” he says. “And the rooms have to be completely airtight. They must not leak.”
Regulating pressure in the rooms was no easy task, partly because the VHP decontamination system was integrated in each room. This one-of-a-kind VHP system was developed and programmed by KeyPlants automation experts.
“Distributing the hydrogen peroxide through the ventilation ducts is not the way you usually do it,” Olle explains. “Typically, you have a small machine that you wheel into the room and then start a disinfection cycle. But in this case, it’s fully automated.”
This meant integrating the system that controls all of the valves, fans, motors, etc. in the cleanrooms with another system that controls the actual environmental with pressures temperatures in the plant. “These had to be integrated into our client’s overall system and also with certain vendor systems, as well as with the filling line, which is a very advanced piece of equipment,” Olle says. “So, all these systems have to communicate and work together, but they were made by different vendors and that is always very complicated.”
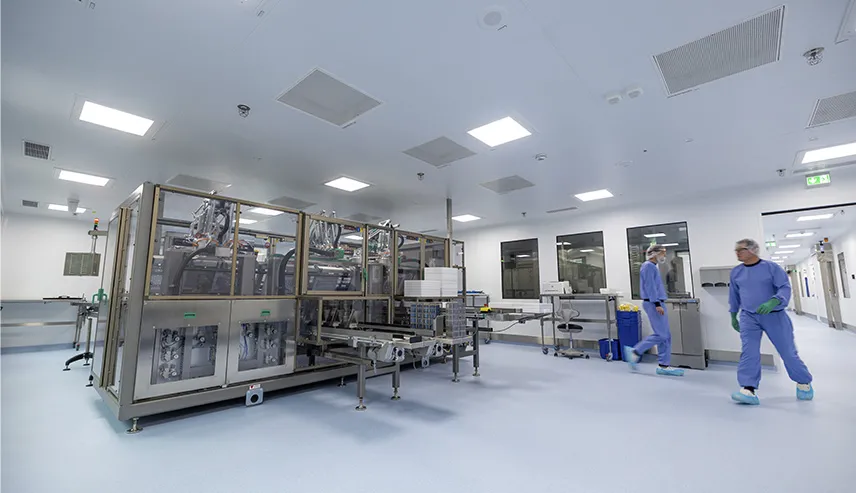
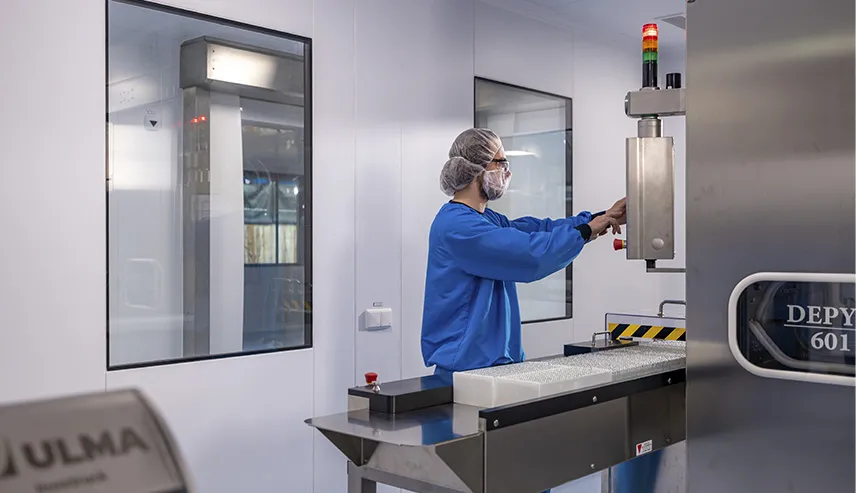
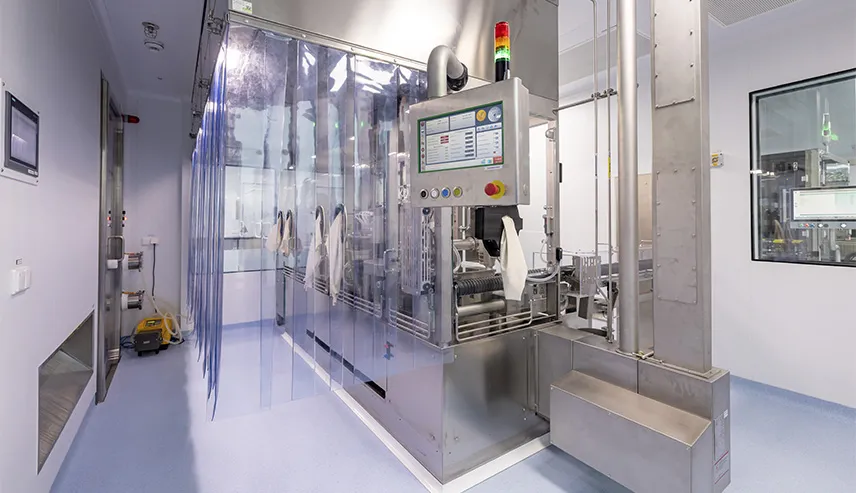
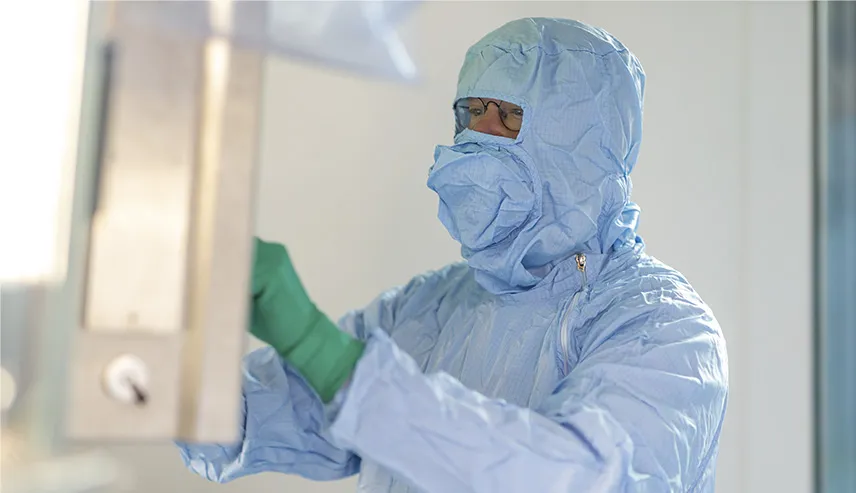
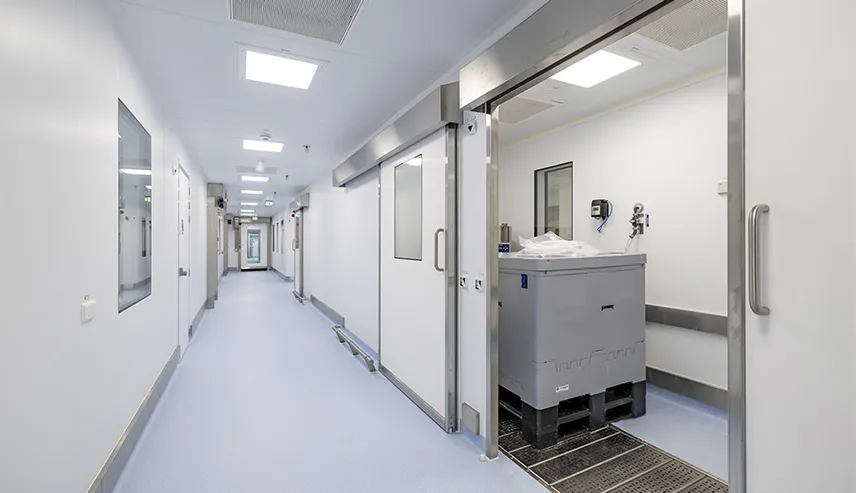
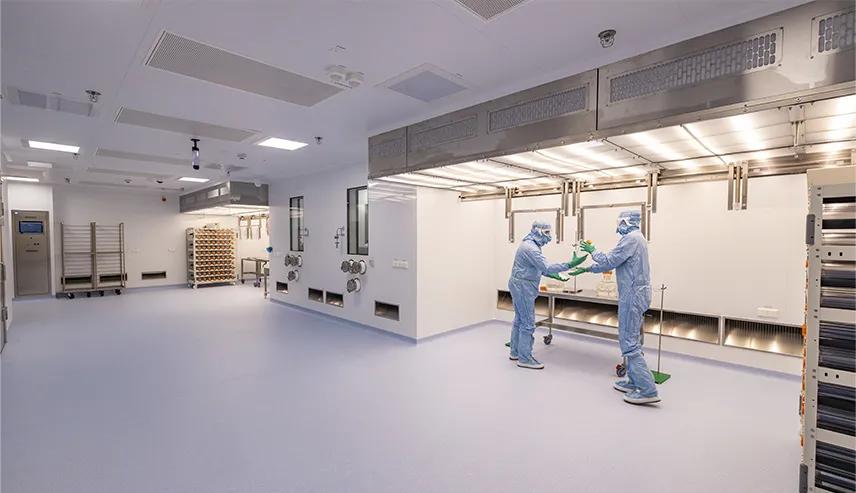
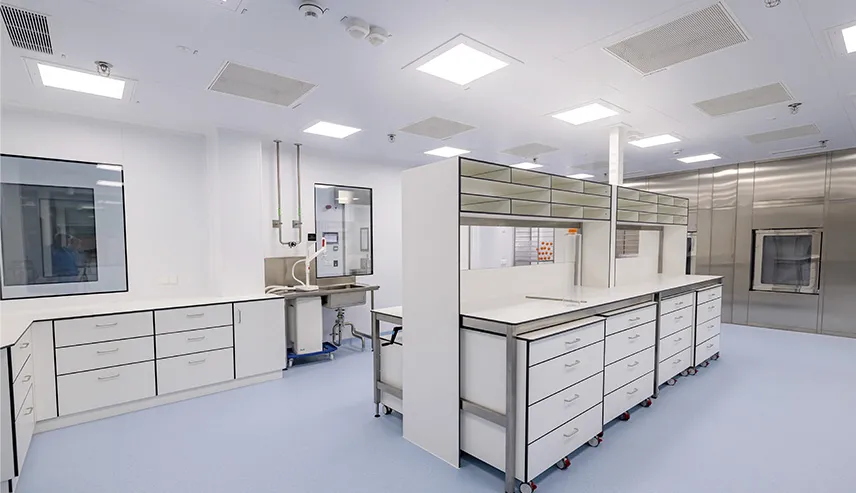
Joint problem-solving
Joint problem-solving
The challenges unfortunately led to some delays. Fortunately, though, the client and KeyPlants established a level of trust during the project that enabled the teams to overcome the challenges together for a highly successful outcome that drew praise from the client.
“We are proud of our new state-of-the-art modular production facility that enables us to meet our increasing sales volumes,” says the client’s Manager of Engineering & Capital Project Lead. "Adding this modular building to our existing production building in limited available space was a great challenge, but nevertheless a successful achievement."
It was quite a journey for both KeyPlants and the client. “With this new technology, there was no pre-existing best practice,” Olle says. “So, working closely with the client, we found ways of solving the problems, automating the systems, and getting the plant up and running.”
![]() | ![]() |
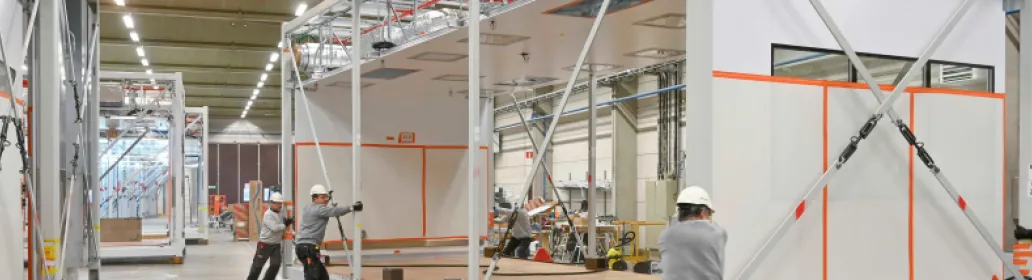